Wiring: When 'just right' is too big??
Moderator: Jim Walsh
Wiring: When 'just right' is too big??
After a number of discussions and liberal libations, we have tackled our wiring problem(s). We are replacing all the mast wiring, both in the mast and inside the cabin. Everything else seems to be OK, although we're cleaning up the panel, e.g., adding a new terminal strip so the ONE ground post will no longer look like two wrestling octopi trying to pin one another. . .
Thanks to encouragement and tips from this board, we HAVE got all our new wiring pretty much in place. The problem is, we're doing this based on Don Casey's recommended specs, and--compared to what was there before--our wires are HUGE: think spaghetti (old: 14 gauge, we think, and very skinny coax) compared to penne (new: 12 gauge + 1/2" dia. coax).
Inside the boat, that has simply meant enlarging the existing passageways or making new ones. We're having a problem, though, with the triplex that goes up to the existing combo steaming/deck light fixture at mid-mast. The terminal screws in the Aqua Signal fixture are teensy; the wiring is big and fat (and at one point, we need to get TWO wires onto a tiny screw. . .). Does anybody have a suggestion on how to make this work?"
Thanks to encouragement and tips from this board, we HAVE got all our new wiring pretty much in place. The problem is, we're doing this based on Don Casey's recommended specs, and--compared to what was there before--our wires are HUGE: think spaghetti (old: 14 gauge, we think, and very skinny coax) compared to penne (new: 12 gauge + 1/2" dia. coax).
Inside the boat, that has simply meant enlarging the existing passageways or making new ones. We're having a problem, though, with the triplex that goes up to the existing combo steaming/deck light fixture at mid-mast. The terminal screws in the Aqua Signal fixture are teensy; the wiring is big and fat (and at one point, we need to get TWO wires onto a tiny screw. . .). Does anybody have a suggestion on how to make this work?"
To unpathed waters, undreamed shores.
The Winter’s Tale. Act iv. Sc. 4.
The Winter’s Tale. Act iv. Sc. 4.
-
- Posts: 3535
- Joined: Feb 5th, '05, 20:42
- Location: '66 Typhoon "Grace", Hull # 42, Schooner "Ontario", CD 85D Hull #1
Wiring
Judith,
Check out the variety of crimp terminals. Usually flat ring or open (forked) terminals are flat enough to put several conductors under one terminal screw.
Another thing that can be done is to splice both conductors to a third tail. The tail (smaller gauge) can attach to the contact screw.
Good luck.
O J
Check out the variety of crimp terminals. Usually flat ring or open (forked) terminals are flat enough to put several conductors under one terminal screw.
Another thing that can be done is to splice both conductors to a third tail. The tail (smaller gauge) can attach to the contact screw.
Good luck.
O J
"If I rest, I rust"
Voting Member #490
Voting Member #490
Re: Wiring: When 'just right' is too big??
The Twelve Volt Bible agrees with that. In fact, they recommend 10 gauge (canneloni?Judith wrote:...The problem is, we're doing this based on Don Casey's recommended specs, and--compared to what was there before--our wires are HUGE: think spaghetti (old: 14 gauge, we think, and very skinny coax) compared to penne (new: 12 gauge + 1/2" dia. coax)....

I would use a pair of ring terminals on the screw.Judith wrote:...The terminal screws in the Aqua Signal fixture are teensy; the wiring is big and fat (and at one point, we need to get TWO wires onto a tiny screw. . .). Does anybody have a suggestion on how to make this work?"
If 10-12 gauge wire won't fit in the other end of the terminals, fit in the biggest size you can. Then cut those wires short and join them to your 10-12 gauge wires with Step-Down Butt Connectors.
Makes sense?

-
- Posts: 839
- Joined: Feb 8th, '06, 18:30
- Location: Canadian Sailcraft 36T
If you go LED
If you go LED nav lights you can reduce the wire size. I would not reduce the VHF cable though..
This is one of my favorite on-line calculators. it sizes marine wire..
http://boatstuff.awardspace.com/awgcalc.html
This is one of my favorite on-line calculators. it sizes marine wire..
http://boatstuff.awardspace.com/awgcalc.html
Re: Wiring
If you do the "splice" I would recommend soldering the joint well. Heck, I would also do that with crimp connectors on the mast since you probably won't get a chance to check them carefully for some time... (ain't it great sailin' in FL...Oswego John wrote:Judith,...
Another thing that can be done is to splice both conductors to a third tail. The tail (smaller gauge) can attach to the contact screw.
O J

-michael
-michael & Toni CDSOA #789
s/v KAYLA CD28 #318
2012 FLSTC Heritage Classic
Niceville FL
+30° 30' 24.60", -86° 26' 32.10"
"Just because it worked, doesn't mean it works." -me
No shirt + No shorts = No problem!
s/v KAYLA CD28 #318
2012 FLSTC Heritage Classic
Niceville FL
+30° 30' 24.60", -86° 26' 32.10"
"Just because it worked, doesn't mean it works." -me
No shirt + No shorts = No problem!
- Steve Laume
- Posts: 4127
- Joined: Feb 13th, '05, 20:40
- Location: Raven1984 Cape Dory 30C Hull #309Noank, CT
- Contact:
- Warren S
- Posts: 254
- Joined: Jul 27th, '06, 21:22
- Location: s/v Morveren
Cape Dory 270 Hull #5
Washington, NC
Hmmm. I need more
I would be interesting in any supporting info in Steve's observation. Given that Type III (solder-tinned) cable is specified for marine environments, I naturally am convinced that terminations should be soldered...
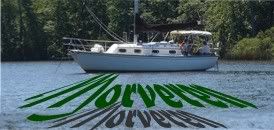
"Being hove to in a long gale is the most boring way of being terrified I know." -Donald Hamilton
-
- Posts: 3535
- Joined: Feb 5th, '05, 20:42
- Location: '66 Typhoon "Grace", Hull # 42, Schooner "Ontario", CD 85D Hull #1
Soldering Vs Crimping Electrical Terminals
I would hope to never be accused of any objection in regard to soldering electrical terminals. I think that it is also proper to mention, at this time, the merits of a properly crimped termination by a quality, calibrated crimping tool. The following thoughts are not to say that one method is better than the other. There are mostly pros and a few cons concerning each way. The most common fault, in my estimation, is a "cold" solder joint, especially in electronic wiring. Very hard to detect with the naked eye.
Both methods are accepted, the choice usually being predicated by the particular job specs. Many jobs under the aegis of both governmental and private industrial standards both allow and encourage crimped terminations. Crimped, as well as soldered terminations are permitted by NEC (Elect. Code) and AEC.
The major problem with using soldered joints is the type and amount of heat applied. A dry heat should be used, ie an electric soldering gun or a pencil tip iron. Avoid open flame heat. Soldering flux must be used. Excessive heat can produce cupric oxide which will compromise the joint.
A common method of wiring a fixture, mentioned earlier, is to use a fixture tap. This is accomplished by splicing the heavier load bearing wires together with a smaller gauge wire (fixture tap). The small wire attaches to the fixture while the larger wires maintain the load without endangering any voltage drop.
A word of caution. When wiring a mast or anything subject to vertical gravity pull, at each fixture location a method of mechanical support should be incorporated to suspend the weight of the conductors while allowing the splices and termination points to remain free floating.
I highly recommend that you review a compilation of good, bad and ugly mechanical crilping tools forwarded to us by Maine Sail. I consider it a very comprehensive, educational and informative review. Thanks again, Maine Sail.
http://www.pbase.com/mainecruising/wire_termination
O J
Both methods are accepted, the choice usually being predicated by the particular job specs. Many jobs under the aegis of both governmental and private industrial standards both allow and encourage crimped terminations. Crimped, as well as soldered terminations are permitted by NEC (Elect. Code) and AEC.
The major problem with using soldered joints is the type and amount of heat applied. A dry heat should be used, ie an electric soldering gun or a pencil tip iron. Avoid open flame heat. Soldering flux must be used. Excessive heat can produce cupric oxide which will compromise the joint.
A common method of wiring a fixture, mentioned earlier, is to use a fixture tap. This is accomplished by splicing the heavier load bearing wires together with a smaller gauge wire (fixture tap). The small wire attaches to the fixture while the larger wires maintain the load without endangering any voltage drop.
A word of caution. When wiring a mast or anything subject to vertical gravity pull, at each fixture location a method of mechanical support should be incorporated to suspend the weight of the conductors while allowing the splices and termination points to remain free floating.
I highly recommend that you review a compilation of good, bad and ugly mechanical crilping tools forwarded to us by Maine Sail. I consider it a very comprehensive, educational and informative review. Thanks again, Maine Sail.
http://www.pbase.com/mainecruising/wire_termination
O J
"If I rest, I rust"
Voting Member #490
Voting Member #490